「革のダイヤモンド」とも称されるコードバン。馬のおしりの部分にしか存在しない希少な革で、宝石を思わせるような光沢、それに掌に吸い付くような滑らかな手触りと高い耐久性が特長です。革好きの方にとってはたまらない素材なのではないでしょうか。
このコードバンを原皮(生の状態の皮)から鞣(なめ)して製品革に仕上げることのできるタンナーは、世界でたったの2社しかないと言われています。1社はアメリカのホーウィン社、そしてもう1社がおわすのは、何と日本! 今回は日本随一の革どころ、姫路に工場を構えておられる馬革専門のタンナー、そしてコードバンをイチから鞣すことのできる数少ないタンナー、新喜皮革さんをご紹介します。
革の工場見学に行ってきました
鞄工房山本のランドセルの一部のモデルにも、新喜皮革さんのコードバンを使用させていただいています。そんなご縁もあって、この度はスタッフの研修として新喜皮革さんの工場を見学させていただく機会に恵まれました。
この日の参加者は製造スタッフも販売スタッフも入り乱れ、30人程となかなかの大所帯です。新喜皮革さんに到着すると、まずは革について、新田専務からお話を聞かせていただきました。
「製品革の元となる原皮は食肉用の動物から取られた皮です。鞣す目的は腐らないようにすること。自然の恵みを粗末にせず、長く使っていけるようにすることです」と新田専務。改めて、革が自然からの頂きものであることを思いました。
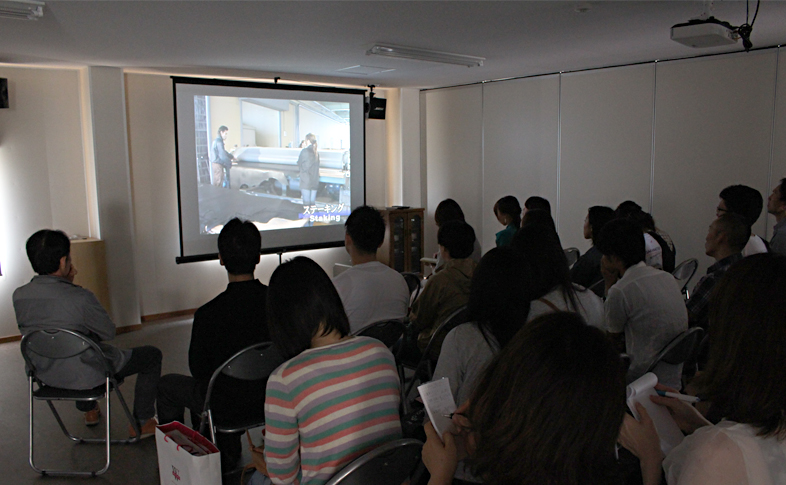
次いで工場見学の前に、鞣しの解説用DVDを見ながらの予習です。
「皮」を「革」にするためには、非常に多くの工程が必要であるとのこと。それらの工程は大きく分けると〈1. 準備〉〈2. 鞣し〉〈3. 仕上げ〉という3つの段階になっています。こうした工程の中で、「皮」から表皮や毛、肉の部分にあたる皮下組織を取り除き、保存性などに優れた真皮層だけを残して、「革」へと変化させていくわけです。
鞣しの大まかな流れが掴めたら、次は現地実習です! はやる気持ちを落ち着かせながら、スタッフ達はぞろぞろと敷地内の工場へ移動していきました。
生のままの皮は強烈でした
工房見学は、鞣しに取り掛かる前の「準備」の工程から始まりました。この工程では、原皮から不要な部分を除去するなどの下ごしらえ的な作業が主で、後に続く鞣しの工程を行いやすくするのが目的です。
広く開いた工場の入口に差し掛かると、まず目に飛び込んできたのは高く積まれた原皮の山。大人の胸くらいの高さまで積み上げられた皮のブロックが、いくつも置かれていました。
目で見るより先に感じたのは、その匂い! お酢のような酸っぱさに生臭さがミックスされたような、他では嗅いだことのない独特な匂いが立ち籠めています。新喜皮革さんで扱っている馬皮はポーランドやフランス、イタリアなどヨーロッパ産のものが中心ですが、それらの原皮は海を越える間に腐ってしまわないよう塩漬けにされて、水分を飛ばした状態で輸送されるとのこと。この強烈な匂いは入念な保存加工の証しなのでしょうね。
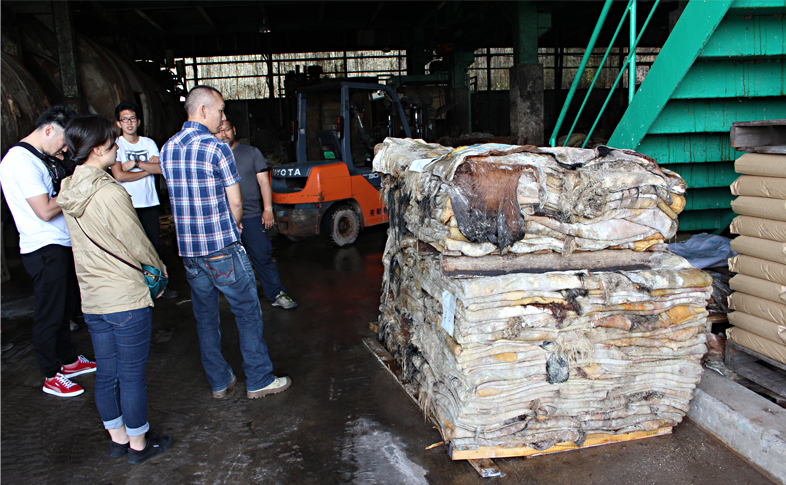
写真右の塊が塩漬けされた原皮です。
馬から採られたままに生々しく毛や肉が残り、塩の結晶もたくさんついています。
工場に届いた原皮は馬一頭丸ごとのサイズですから、まずはお尻の部分とそれ以外に切断されます。部位ごとに繊維構造が異なっているので、それぞれに適した鞣しを行うためです。
切断というと簡単そうですが、きれいに分割するためにはそれ相応の技術が必要とのこと。これも職人の仕事ですね。
水で洗って革の塩抜き
次は「水洗い」です。原皮が置かれている区画の壁に面して、見上げるばかりに巨大なドラムが並んでいました。このドラムに原皮と水を入れて回転させることで、原皮から塩分や汚れを取り除き、同時に水分を含ませて生の皮の状態に戻していきます。
この日は水洗い用のドラムは動いていませんでしたが、大きなドラムが一斉に回っている光景は、きっとすごい迫力でしょうね。
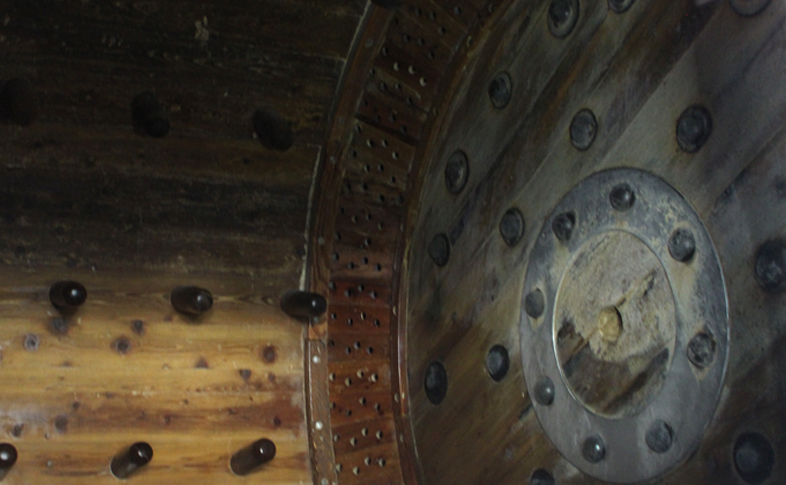
ドラムの内部には一面に突起が配されています。ドラムを回すとこの突起に皮が引っ掛かって持ち上がり、てっぺんから落として叩きつけることによって、皮を強く揉み洗いするような仕組みになっています。ちなみに、ドラムは木製です。
水洗いによって、原皮が生の状態に戻りました。それからは表皮や毛、肉などの不要な部分を機械で削って取り除く作業や、皮を表裏で分割して厚みを整える作業などを経て、ようやく準備の工程が完了となります。革の鞣しは、想像以上に手間の掛かる仕事のようですね……。
鞣しにもいろいろあるのです
鞄工房山本スタッフ達が列をなして、初めて見る光景にきょろきょろしながら、どんどん工場の奥へと進んでいきます。
ここからはいよいよ「鞣し」の工程に入ります。この工程では原皮に薬剤や油を用いて処理し、時間が経っても腐らないようにするための加工を行います。この工程を経て、「皮」から「革」へと呼び方が変わるわけです。
革はその鞣し方によって、大きく三つの種類に分かれます。
その一つが〈クローム鞣し〉。後述するタンニン鞣しに比べて柔軟性や耐熱性、生産効率に優れ、色を染めた際の発色の良さが特徴です。
二つ目が〈タンニン鞣し〉です。ピットという大きな水槽に皮を浸して鞣す、古代エジプト時代からの歴史ある製法と、クローム鞣しと同様にドラムを回して鞣す製法の二通りがあります。どちらにせよ、クローム鞣しの革に比べて硬く、染色性も劣るのですが、一方で独特の風合いを持っており、経年変化でますます味わい深い表情になっていくという、機能性を超えた魅力を持っている革なのです。
三つ目は、クローム鞣しとタンニン鞣しの手法を合わせた〈混合鞣し〉です。混合鞣しによる革は、タンニン鞣しの風合いと、クローム鞣しの柔軟性、耐久性を併せ持った性質に仕上がります。
タンニン鞣しに使われる「鞣し剤」の原料はタンナーによっていろいろですが、新喜皮革さんでは、アカシアの木の表皮から抽出されたタンニン(ミモザ)を使用しているそうです。
冒頭でもご紹介したコードバンは、新喜皮革さんではすべてタンニン鞣しで、それも手間と時間の掛かるピット製法によって作られているそうです。美しい素地を最大限活かす加工をされているのですね。
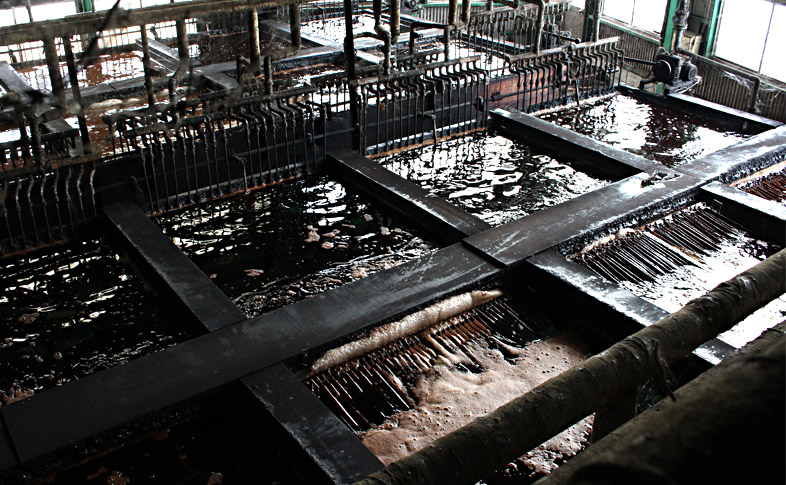
大人が中で寝転べるくらい大きな水槽がぎっしりと並んでいます。これらの水槽やドラムは木製で、専門の職人によって作られているそうです。
ピットには、ちょうどコードバンが浸かっていました。
ピットは内部に配された銅管によって水温を保ちつつ、鞣し剤をかき混ぜながら24時間稼動しています。コードバンの場合、段階的により濃度の高い鞣し剤の水槽へと移し替えられながら、1ヶ月もの時間を掛けて鞣されていきます。
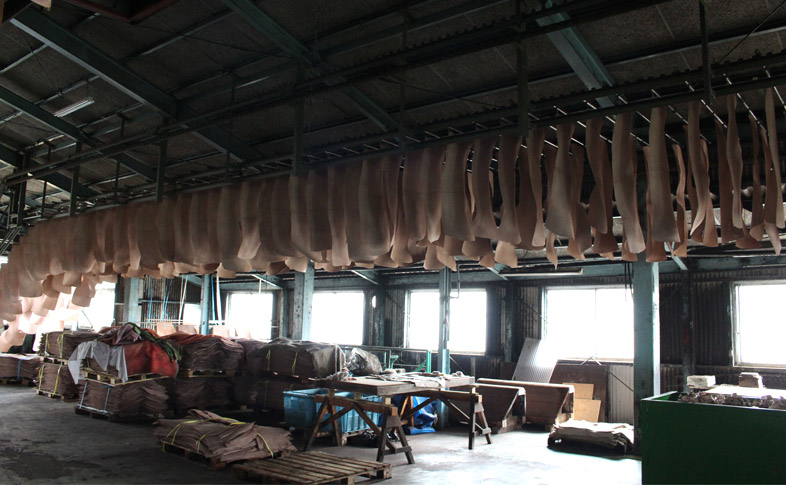
工場の2階へ上がると、天井の一角に垂れ下がった革が風にそよいでいました。妙な光景です。これは鞣した革を乾燥させているのだそうで、天井にぶら下げているのは省スペース化のための工夫とのこと。この日は天井の一部に革が並んでいるだけでしたが、それでもすごい枚数でした。
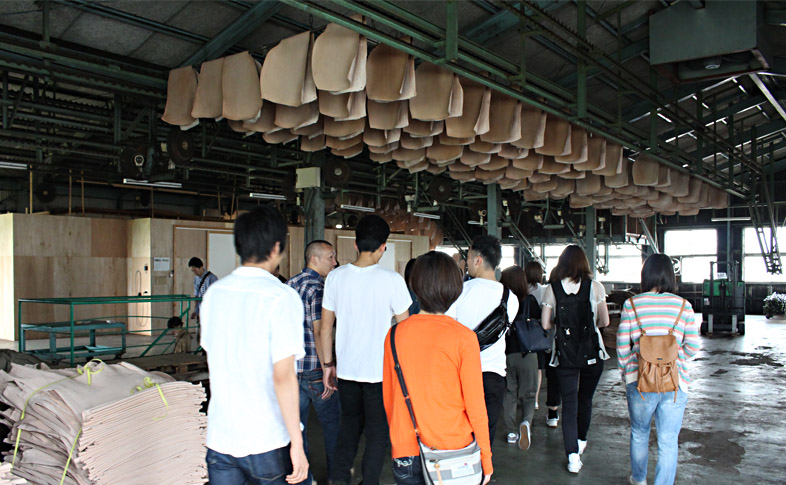
鞣し上がったコードバンはこうして10日間ほど乾かし、乾燥場から下ろしてからも更に3ヶ月ほど(!)寝かせます。長く寝かせることで鞣し剤が革により馴染み、柔軟性を増すのだそうです。
100枚からたったの5枚!? とても希少なランドセル用コードバン
乾燥が終わったコードバンを目の前で広げながら、新田専務にコードバンの性質についてお話を伺いました。
「コードバン」と呼ばれる部分は、実は皮の表面ではありません。コードバンの繊維層は、革の銀面層と網状組織層との間に、ほんの1~2mmくらいの厚みで存在しています。そのわずかな部分を「裏削り」という作業で革の裏側から慎重に削り出していくことで、やっとコードバン層との対面が叶うのだそうです。
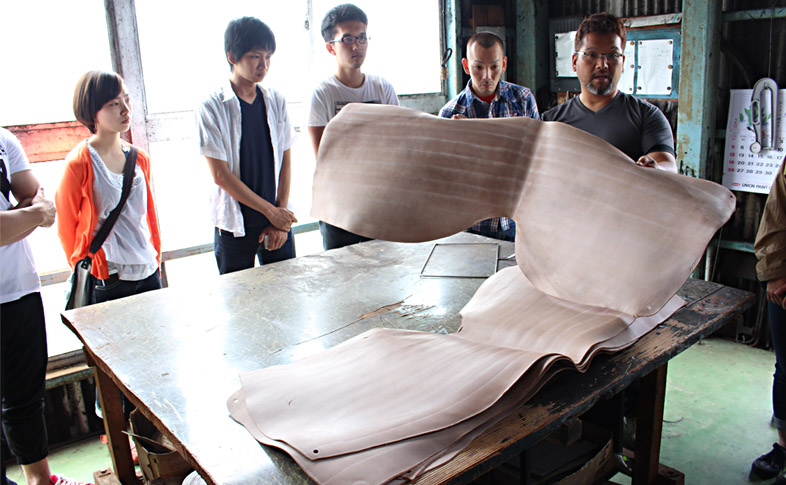
コードバンの裏削りには卓越した技術が必要で、これを身につけている職人さんは日本でも数人しかいらっしゃらないんだとか。革の加工に限らず、薬品の管理などあらゆる過程に技術と経験が必要で、些細なミスでも革が台無しになってしまうため、とても気を遣って作業されているとのことでした。
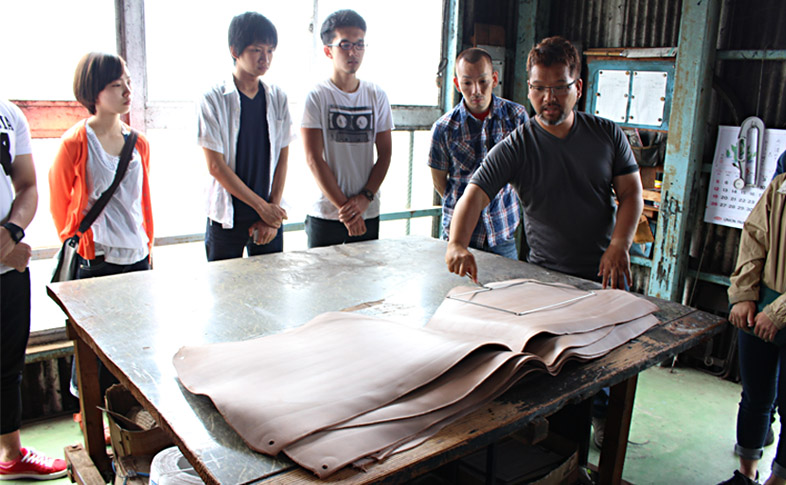
コードバンを削り出した革に、ランドセルのかぶせの型をあてて見せていただきました。
コードバンはすべての馬から採れるわけではありません。また、採れたとしても、そのサイズは馬によってまちまちです。ランドセルのかぶせは面積が大きいため、ランドセル用に使うことのできる革は、コードバンが100枚あったとして4~5枚がせいぜいのところだそう。私たちが日々何気なくランドセルに仕上げているコードバンは、想像を超えて選び抜かれた逸品だったようです……!
サイズや状態によって選別が済んだ革は、日光などの紫外線で焼けて色ムラができないよう保管用の暗室に運び込まれ、しばし次の工程の順番が回ってくるのを待つことになります。
染色で鮮やかに、加脂でしっとりと
「仕上げ」の工程では、多くの手法を組み合わせて、鞣し上がった革が顧客からの依頼に応じた色や風合いになるよう加工をしていきます。
最初に対面したのは染色と加脂の工程でした。〈染色〉では、これまた巨大なドラムに革と染料を入れて回すことで色をつけます。染料の量や配合、ドラムを回す時間で仕上がりの色はまったく違ってきますので、ここにも深い知識と経験が必要となります。
〈加脂〉というのは、鞣しの過程で革から油分が抜けてしまうのですが、加脂剤を入れることによって革に油分を充填する作業です。そうすると、すっかり乾燥していた革に潤いが戻り、柔軟性が出て手触りも滑らかになって、私たちが知っている革の質感に近づいていきます。
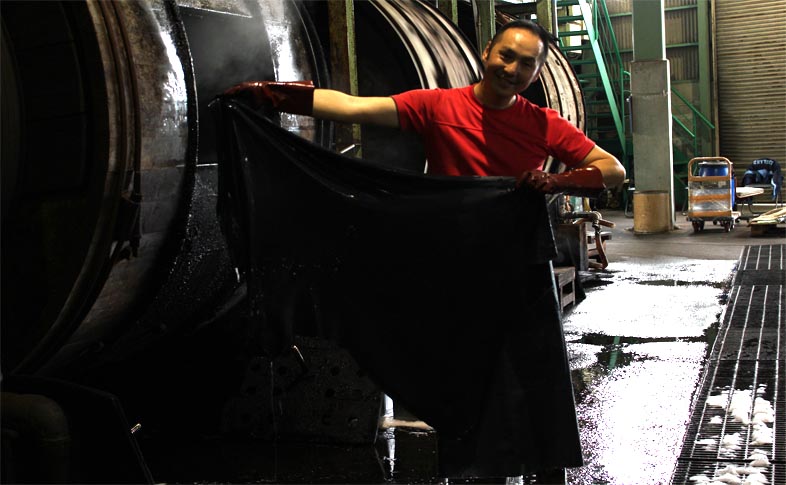
影になってしまっていますが、グレーに染色し終わったところの革を、ドラムから取り出して見せてくださいました。染色の際には熱を加えるので、ドラムから湯気が立ち上っていますね。

染色し上がった革は余計な水分を含んでいるので、大きなローラーで水絞りをして伸ばします。
染色工程で水気を含んだ革を再び乾燥させ、ようやく最終の工程に入ることができます。
「宝石のような輝き」の要、グレージング
更に場所を変え、仕上げの工程を順番に見せていただきます。
革表面の表情を決めるには何種類もの手法がありますが、コードバンに最もよく用いられるのが「グレージング仕上げ」です。これはガラス製の棒で革表面を磨く手法で、専用の機械にコードバンをかけると、見る間に表面の艶が増していくのが分かります。
どういう理屈かというと、通常の革は繊維組織が革表面に対して水平に走っているのですが、コードバンの場合は特殊で、表面に対して繊維組織が垂直に立っているような格好です。素の状態だといわば細かく毛羽立っているようなもので、光も乱反射して散らしてしまいますから、このままだと輝きは微塵も見えません。そこへ、滑らかなガラスの棒で革表面を強くこすっていくと、毛羽立っていた毛先が寝かしつけられ、見違えたように美しい艶が生まれるというわけです。
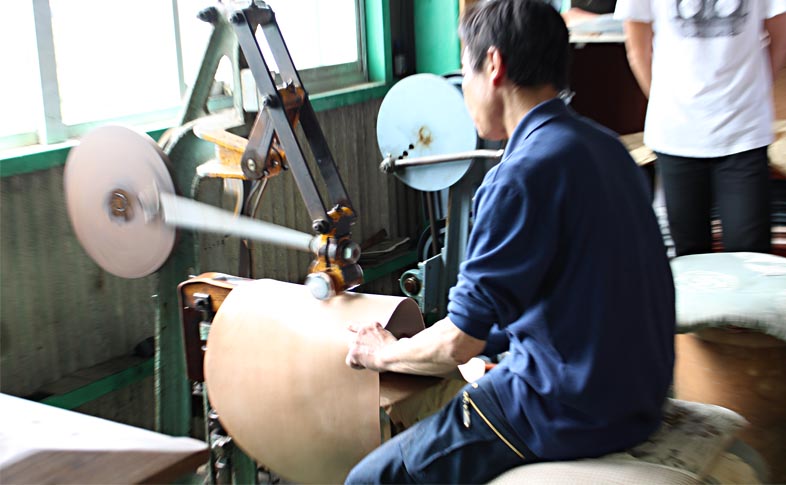
グレージング用の機械です。革に接している部分がガラス製になっており、これが機械のアームで前後にぐいぐいと動いて革を磨いていきます。
踏ん張っていないと革ごと持っていかれそうな力強さです。
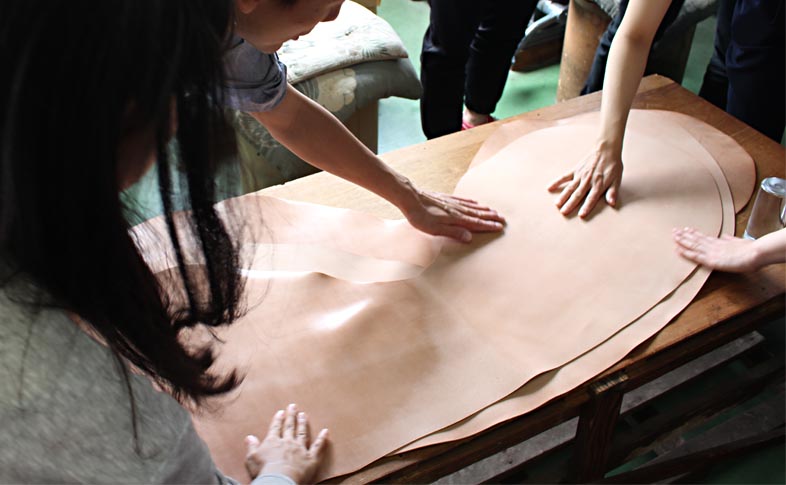
右半分が素のまま、左半分がグレージング加工を施された状態です。目で見ても艶の違いは明らかでしたが、撫でてみるとキュッキュと音が鳴りそうなほどのツヤ感。あまりの違いに歓声が上がりました。
グレージング加工されたコードバンは、コードバン層の部分とそうでない部分が分かりやすくなっています(上の写真でも境界線が見えますね)。別の作業台へ移ると、職人さんたちが並んで素早い手捌きで、革からコードバン以外の部分を切り落としていました。
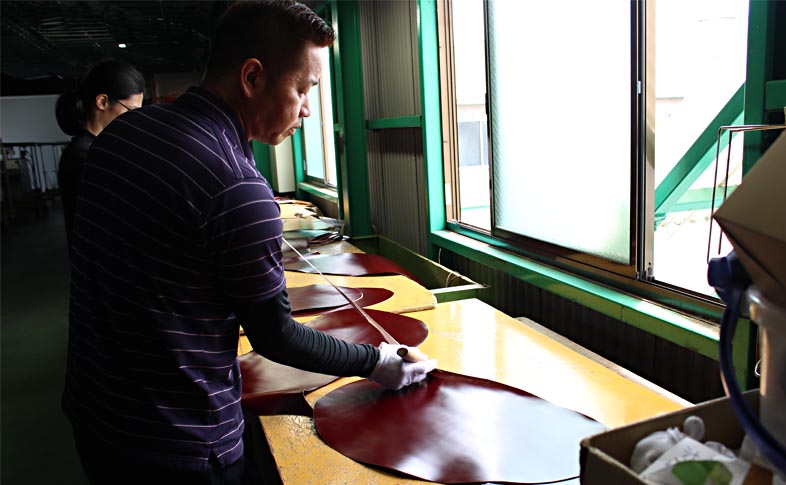
分かりやすいと言っても、色がついていると素人目には厳しいです。職人さんたちは迷いなく刃を走らせていました。
革の最終的な風合いはここで決まる、「塗装」
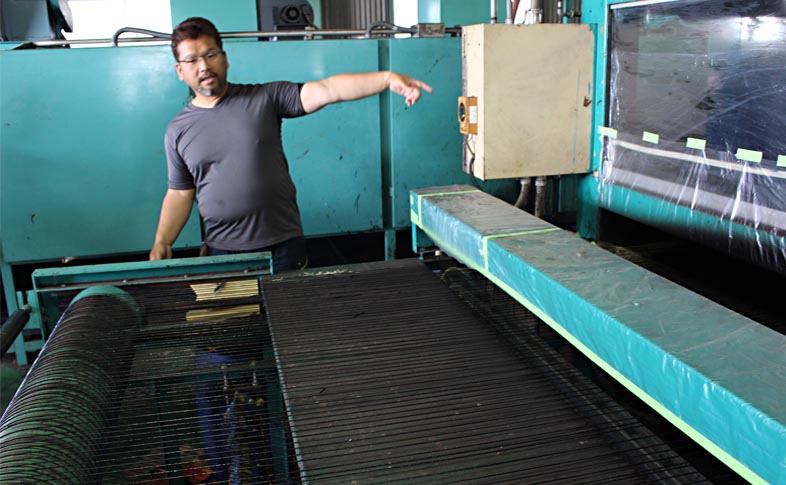
更に場所を移すと、またも大きな空間に出ました。部屋の端から端までを占領している大型の設備は、革の塗装をするための機械でした。
機械の中を、ゴム紐を並べたようなベルトコンベアが走っています。ここに革を載せて機械へ送り込むと、まずはセンサーが革の形を読み取り、その範囲に塗料を吹きつけます。ゆっくり機械の中を通る間に乾燥させ、終わると革が機械の反対側から出てきます。ここまでがすべて自動で行われます。
今でこそ機械の導入によって自動化されていますが、昔はこれらの工程をすべて手作業で行われていたそうです。
コードバンの塗装はというと、通常の革用の機械ではなく、コードバン専用の塗装機が用いられます。塗装機が設置された、コードバンだけを扱う部屋に移動してきました。
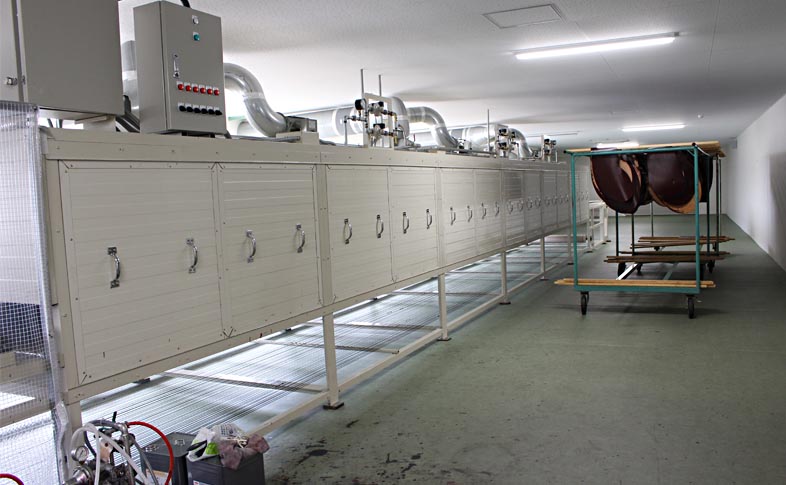
こちらの塗装機には、小さな埃も入り込まないよう、ぴっちりとカバーがされていました。コードバンの場合、塗装の工程が10回にも渡って繰り返されます。本当に特別扱いです。
仕上げの過程でコードバンが水分を含むと艶が損なわれてしまうため、湿度の高い梅雨の時期などは、一般的には製造ができなくなるものなのですが、新喜皮革さんの設備ではそれが可能になっています。この部屋は温度と湿度が常に一定に保たれており、一年を通して最高のコンディションでコードバンの塗装を行えるようになっているのです。良いものを生み出すための環境が、徹底して整備されていました。
部屋の温度がコントロールされているとのことですが、その甲斐あってのぼせるような暑さです! 革に最適な温度は、人にはあまり優しくない様子……。鞄工房山本のスタッフも汗をだらだら流しながらの見学です。ここでの作業にはかなりの体力を要するはず。塗装担当の皆さま、お体にはお気をつけて。
こちらの部屋の一角には、塗装が済んで乾燥中のコードバンが並んでいました。
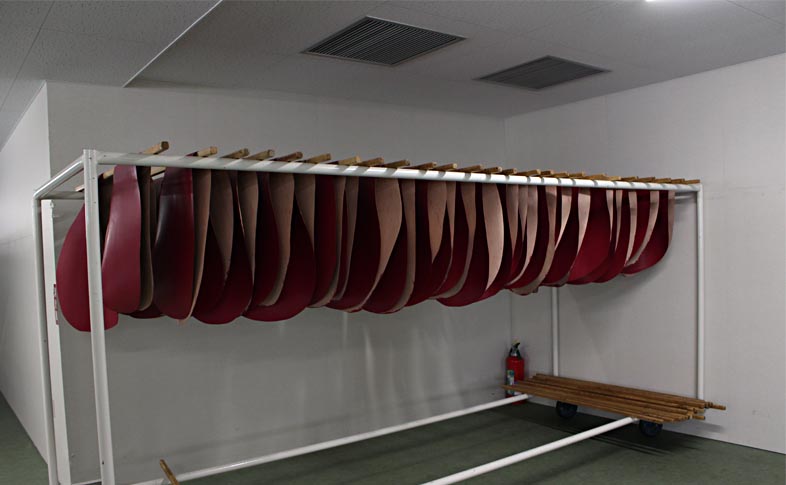
おや? 見覚えのあるような色ですね……。
気付いた方もいらっしゃるでしょうか、こちらは鞄工房山本のランドセル、「コードバン・グレース」のローズピンク用に製作していただいたコードバンです!
本当に、本当に長い時間とたくさんの手間を掛けて、一枚の革が完成するのですね……! 気付いたスタッフからは感嘆の声が漏れました。このコードバンは2日後には製品革として発送していただけるとのことで、何やら到着がとても楽しみです。新喜皮革さん、本当にありがとうございました。
最後に
とても長い記事になってしまいました。最後までお付き合いいただき、ありがとうございます。
今回は一息に鞣しの工程をご紹介しましたが、実際にコードバンが原皮から革に仕上がるまでには、実に10ヶ月もの時間が掛かるそうです。その間に、この記事でご紹介しきれなかった工程も含めて、いくつもの段階を踏んで製品革として完成し、やっと鞄工房山本の工房へ到着することになります。
工房の倉庫にまとまって保管されている革を見ていると、つい忘れそうになってしまいますが、どの革も一枚ずつを丁寧に、大切に仕上げていただいていること、改めて思い直しました。良い素材を提供してくださるタンナーさんの存在があってこそ、私たちはランドセルをつくることができるのですね。
皆さまのお手元にランドセルが到着しましたら、素晴らしい革を作り出してくださったタンナーの方々にも思いを馳せていただけると、同じものづくりの企業として嬉しく思います。
どうもありがとうございました。